ABOVE: Stockyard Industries supplied and installed 168 freedom-style mating stalls with lifting back gates, plus a Big Dutchman automatic feedline and six-tonne silo.
Victorian-based producer Grant Kelly and his family have been involved in the pig industry for over 50 years, providing them with an understanding of how important it is to have high quality durable equipment and housing for their pigs.
That’s why, when looking to expand, they turned to the well experienced and respected team at Stockyard Industries, which recently completed their new turnkey 168-place dry sow mating shed, and they couldn’t be more impressed with the results.
The new shed is naturally ventilated using Big Dutchman rolling curtains and utilising four stir fans to maximise airflow – all controlled by a Big Dutchman Vento climate computer.
Stockyard Industries also supplied and installed 168 freedom-style mating stalls with lifting back gates, plus a Big Dutchman automatic feedline and six-tonne silo.
The shed also incorporates a small 800mm concrete slatted flush drain behind the stalls to allow for misting over the sows without wetting the open straw-based area at the rear.
When asked of his experience with Stockyard Industries, Grant was pleased to share.
“The team have a vast understanding of everything, from design at the beginning, planning approvals and permits, all the way through to commissioning the equipment at the end of the build,” Grant said.
“With construction starting through the middle stages of the COVID pandemic, there were minor challenges along the way – as you’d expect during those conditions.
“But Cam Ross – Stockyard Industries pig sales manager – and everyone involved went above and beyond to ensure all issues were resolved as promptly as possible and provided us with a smooth and stress-free build, allowing us to focus on our business.
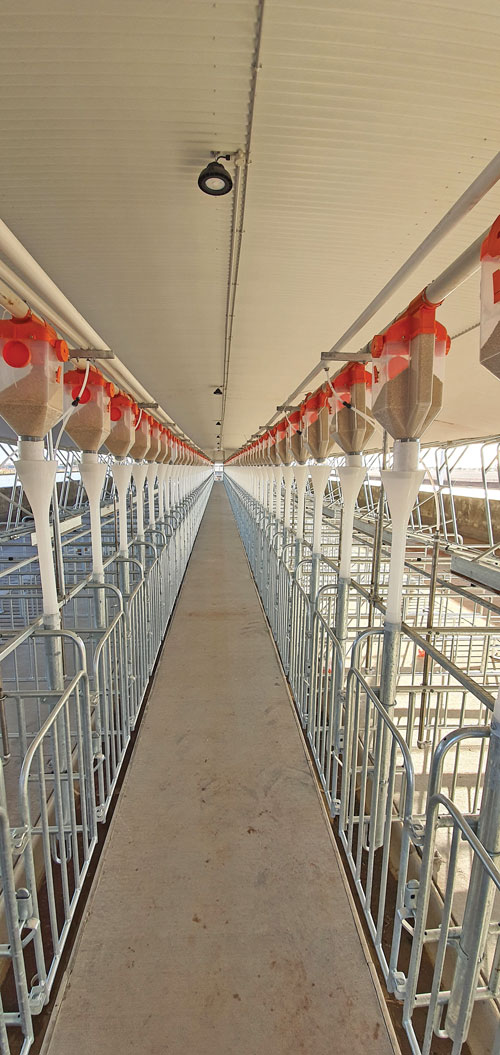
Stockyard Industries recently completed a new turnkey 168-place dry sow mating shed for pig producer Grant Kelly.
“Given the long cold winter we’ve endured, we’ve seen some great evidence of how well the shed is performing.
“Our sows are now maintaining far better health due to no extreme fluctuations in temperature, as previously experienced when housing in eco shelters.
“We’ve also seen that through winter, the sows are staying a lot warmer compared to previous years, so we’ve had to cut back their feed consumption by an average of 1kg per sow each day, to ensure they stay within an optimal weight range for their gestation period.”
As well as cost reductions in feed, Grant said they were able to reduce their overheads by saving labour requirements through automation, which they can now rely on to feed their pigs and keep the shed at a consistent temperature all year round.
“With everything performing exactly as it should, we couldn’t be more impressed,” Grant said.
“The experience and knowledge Stockyard Industries possesses is second to none.
“That’s why we’ve recently engaged them to get our next project underway, which we can do with full confidence, knowing they will achieve our desired results.”
When considering new, refurbished or extensions to production facilities, contact Stockyard Industries today – stockyardindustries.com